Industrial Systems Integration: Leveraging AI for Smart Manufacturing Optimization
Blog
5 Min 52 Sec Read
Not long ago, the idea of machines learning and adapting in real-time seemed like something out of a science fiction novel. However, today, it has become a part of the workflow.
An ice cream manufacturer, for example, has already leveraged advanced algorithms to cut down on their recipe costs. And they did it without sacrificing the quality their customers expect. It’s a clear sign that AI in smart manufacturing isn’t just a trend anymore.
It’s become a strategic shift.
Across different factory floors – whether it’s food processing or the automotive industry – industrial artificial intelligence has transformed –
- How decisions are made
- How problems are predicted
- How resources are optimized
What once required manual oversight and reactive troubleshooting – can now be handled with AI-driven, proactive systems. So, in this article, we’ll break down how manufacturers are applying these technologies to solve everyday production challenges. And there will be some insights into the technology itself too. So, without any further ado, let’s begin.
Why the Factory Floor Is Finally Ready for Intelligence?
The modern manufacturing landscape is anything but simple. It’s evolved into a high-stakes environment where traditional decision-making has become obsolete.
Here’s why –
- Products have become much more intricate, which, in turn, requires management of thousands of variables in real-time
- Skilled labor is in quite a short supply, which leaves only a few experienced operators to steer critical production choices
- Market conditions have shifted rapidly in recent times, which demands immediate, and often unpredictable, responses from the manufacturers
- Supply chains have become more fragile than ever, which may force constant recalibration of production parameters
In such conditions, the expenses for delays, which may be related to materials, lost opportunities, or labor – is extremely high.
So, if you want to counter the same, it’s important to use a system that anticipates everything beforehand and responds accordingly. And that’s what AI-powered manufacturing can do.
With these systems, you can use –
- Real-time detection of anomalies, eliminating the need to wait for post-production quality checks
- Predictive maintenance, preventing downtime before it ever begins
- Intelligent recipe optimization that adjusts based on the specific characteristics of raw materials
- Automated control over process parameters—factoring in hundreds of dynamic variables with zero hesitation
This shift from reactive to proactive operations can help you make smarter, faster, and more precise decisions – precisely when it matters.
Real-Life Applications: Where AI Is Already Driving Results
Let’s look at the ice cream manufacturer’s example again. This organization was working in a volatile market, where commodity pricing shifted frequently and made it impossible to predict raw material expenses.
So, in order to stay competitive, the manufacturer deployed an AI-driven platform that dramatically optimized their recipes using a variety of real-time inputs, such as –
- Up-to-the-minute commodity prices across multiple key ingredients
- Specific quality benchmarks for finished products
- A range of approved substitutes that met quality standards
The results of these steps, needless to say, were impressive. It helped with –
- A 4.3% reduction in total recipe costs
- Consistent product quality across all batches, with zero compromise
- Smarter, data-backed procurement decisions
- Less waste from quality-related product rejections
This isn’t some futuristic proof of concept. It’s AI in smart manufacturing making the most out of your system and delivering a tangible return on investment.
Building the Foundation: What AI Truly Needs to Succeed
While the technology behind AI is undeniably powerful, its success – or failure – depends almost entirely on the foundation you’ve built beneath it. So, without the right groundwork, even the algorithms can fall short.
Here are some tips that can help you build the foundation for AI –
Data Readiness Assessment
Successful AI deployments usually begin with full access to critical datasets, including –
- Machine data pulled from PLCs, IoT sensors, and SCADA systems
- Inspection records and quality control logs
- Supply chain indicators, such as material specifications and properties
- Production planning schedules and historical performance metrics
While you’re at it, make sure you’re not skipping on a data reading assessment. It will affect the performance of AI and how you want to make the assessment work.
AI-Ready Infrastructure
Implementing AI for factory automation usually demands more than just being ambitious. It requires robust and purpose-built infrastructure, including –
- Time-series historians to capture continuous streams of process data
- Centralized data lakes and warehouses for organizing structured and unstructured datasets
- Unified Namespace architectures that streamline data integration across systems
- Edge computing capabilities for instant, real-time data processing
- Secure cloud environments for advanced analytical workloads
Preparing and Cleansing the Data
Raw data coming from factory systems is rarely ready “as is.” So, to make it useful for AI models, manufacturers need to invest their time in –
- Synchronizing time stamps across multiple sources
- Removing noise, gaps, and outlier anomalies
- Normalizing disparate datasets for consistency
- Prioritizing data collected during standard operating conditions
- Adding more context through operational metadata and domain expertise
7 Steps to Implementing AI in Manufacturing
For manufacturers ready to embrace the future, a structured approach is vital.
Drawing from extensive experience across dozens of successful deployments, we’ve crafted a clear, actionable roadmap. Follow these seven steps to ensure your digital transformation in manufacturing leads to real, measurable success.
Dive deeper into AI-driven optimization in smart manufacturing
Define Clear and Impactful Goals
Every initiative you take must begin with a specific, results-driven objective. So, while you are beginning, here are some measurable targets you can set for yourself –
- Reducing unplanned downtime by 25%
- Boosting first-pass yield rates by 15%
- Cutting energy consumption by 10%
- Optimizing raw material utilization by 5%
Without precise goals, it’s quite easy to lose focus or fail to demonstrate the value of the work you are trying to do.
Assess Your Data Landscape
No AI project can succeed without a solid understanding of the data you have available in your store. So, to make some sense out of it, you have to ask –
- What data are we already collecting?
- How accurate, complete, and consistent is it?
- Are there any critical gaps that we need to fill?
- How easily can we access this data for analysis?
Building a strong foundation for industrial data analytics begins in this step. So, you have to ensure that you are not slacking off or taking the wrong step.
Assemble a Cross-Functional Team
AI implementation isn’t and shouldn’t be a solo endeavor. It demands a diverse expertise –
- Domain specialists who live and breathe manufacturing
- Data engineers to curate and prepare raw inputs
- Data scientists to design and train algorithms
- IT professionals to integrate everything securely and efficiently
- Collaboration between these experts is what transforms ambition into execution
Prepare and Cleanse Your Data
Raw manufacturing data can be quite messy sometimes. So, before any meaningful insights emerge, you will need to do the following –
- Address missing or inaccurate values
- Synchronize timestamps across platforms
- Normalize data ranges for uniformity
- Engineer relevant features to enhance model accuracy
Good data preparation is an important part of the process of implementing AI in smart manufacturing and drives powerful machine learning in manufacturing outcomes.
Select the Right Technologies
Apart from everything else, choosing the right tools is also important. However, in this case, you have to consider some specific factors, including –
- On-premises vs. Cloud deployment options
- Batch processing vs. Real-time manufacturing insights
- Pre-built software vs. Customized solutions
- Open-source fireworks vs. Commercial platforms
Remember, there’s no one-size-fits-all answer here. Your choices should be able to fit your specific use case and long-term vision.
Train, Validate, and Refine Your Models
Developing smart and reliable AI models can be quite difficult. However, we have outlined some steps here to make the job a little easier for you –
- Start with collecting historical data to build initial models
- Test rigorously against known outcomes
- Validate performance with live operational data
- Continuously refine the system based on results and feedback
This step is going to be crucial for solutions like predictive AI where readability isn’t going to be optional anymore. It’ll be essential.
Start Small, Scale Fast
As our implementation guide wisely advises, you should always start small by integrating straightforward AI applications to demonstrate value. Here’s how you can do it –
- Pick a well-defined problem with clear ROI potential
- Focus on processes rich in quality data
- Secure stakeholders buy-in early
- Leverage quick wins to build momentum for broader initiatives
Moving Forward with Confidence
The integration of AI in smart manufacturing is no longer a distant possibility – it’s an operational reality. The real question manufacturers must ask isn’t if they’ll adopt AI, but how effectively they’ll harness it. Those who proceed methodically, guided by clear goals and a robust data infrastructure, are already achieving transformative results.
Across industries, we’re seeing AI-driven efficiency improvements reshape the landscape – from predictive maintenance that minimizes unplanned downtime to quality optimization initiatives that boost yields and reduce waste.
Practical AI applications in industry are no longer experimental; they’re delivering measurable ROI and giving early adopters a decisive competitive edge.
The technology is ready. The strategies are proven. And the rewards for those who move decisively are substantial.
For manufacturers seeking to chart their course, our comprehensive guide, “7 Steps to Artificial Intelligence in Manufacturing,” offers a detailed blueprint for success, built from extensive hands-on experience. It breaks down proven implementation strategies, best practices, and real-world insights to help you navigate the journey with confidence.
The future of manufacturing will be shaped by those who can turn data into decisive action. With the right foundation, and the right partners, your journey toward AI-driven transformation doesn’t have to wait. It can start today.
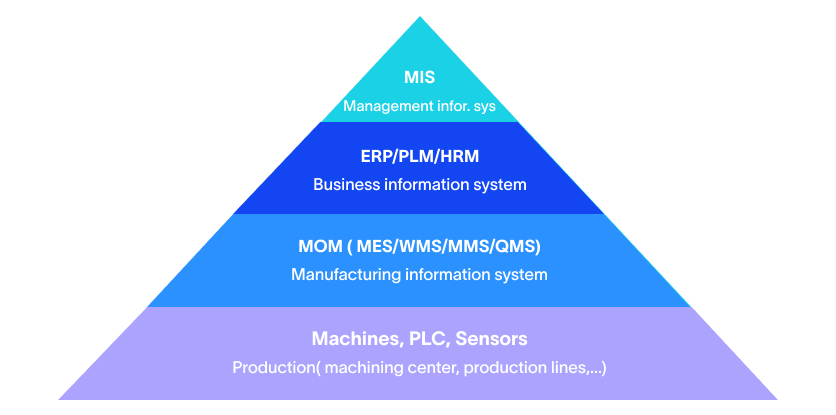
Agile MES: The Key to Unlocking Smart Manufacturing Success
MES is a computerized system used in manufacturing operations to track and document the transformation of raw materials into finished goods. An MES system typically manages and monitors work orders, equipment, materials, and personnel on the shop floor. The system provides real-time visibility into production processes, helps optimize manufacturing operations, and improves the overall efficiency of the manufacturing process.
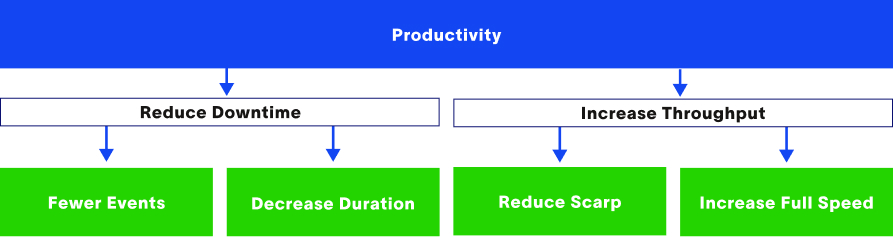
Understanding OEE: The Key to Manufacturing Efficiency
In today’s competitive manufacturing landscape, improving efficiency and productivity is crucial for businesses to remain competitive. One of the key metrics used to measure manufacturing efficiency is OEE or Overall Equipment Effectiveness. In this blog, we will take a closer look at OEE and its importance in manufacturing.
How to Effectively Conduct a Legacy System Integration
Legacy system integration can be a daunting task, but it’s a necessary one for many manufacturers that rely on outdated systems to run their business. Integrating legacy systems with modern technology can improve efficiency, streamline processes, and save time and money. However, it’s important to approach the integration process carefully and methodically to ensure success.
Share on :
Keep On Reading
Subscribe to Our Newsletter
Subscribe to our weekly newsletters to get updates regarding our new production, behind the scene process of our art creation and much more.
After submitting this form you will receive an e-mail with a confirmation link that you must click to complete your request. Detailed information on processing and cancellation can be found in our privacy policy.