CoreM™ - MES Software for Agile Manufacturing
Monitor your production lines with CoreM. Engineered for user confirmability, agility, and efficiency, our MES software seamlessly adapts to evolving production needs, optimizing performance across all manufacturing processes. Commercially and technically scalable, our solutions cater to operations ranging from single lines to multi-plant enterprises, offering integration options from downtime management to full ERP-MES integration.
Empower your decision-making with our Manufacturing Intelligence tools, enabling swift and confident data-driven actions for unprecedented success in today’s dynamic manufacturing environment.
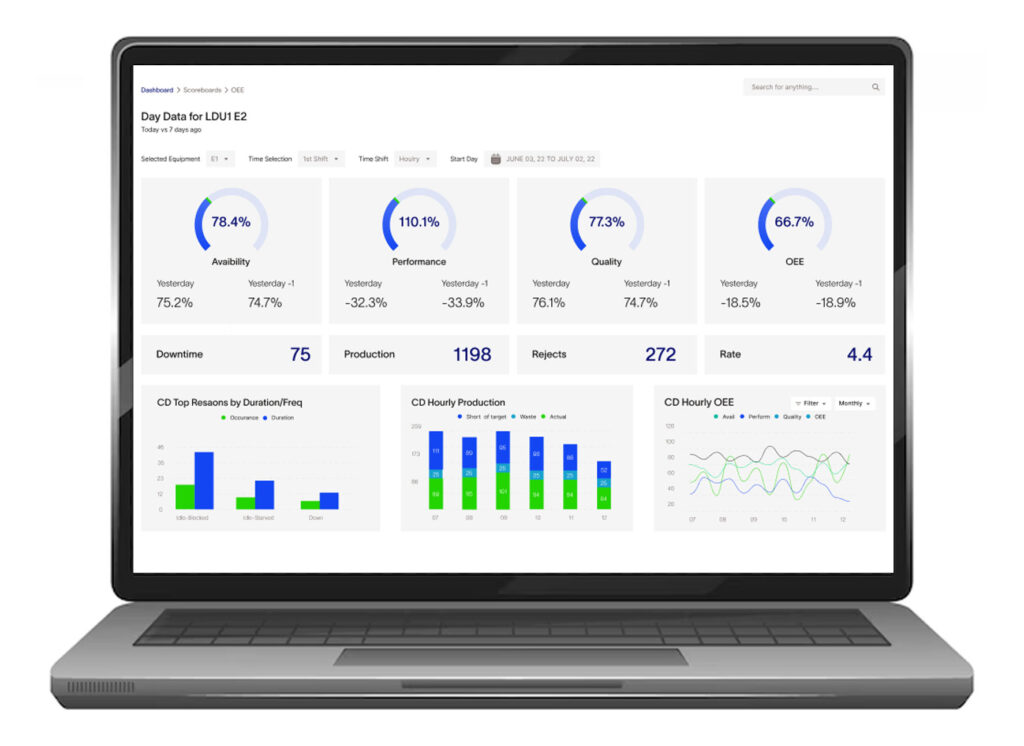
How We Work
Real-Time Performance, Quality, and Production Event Tracking with our MES Software
At its core, CoreM accesses production data from across your plant and integrates with various systems, including PLCs, sensors, manual records, spreadsheets, ERP, and more. This diverse data is transformed into actionable events, each containing detailed information such as conditions, start and end times, quantities, reasons, root causes, and necessary actions.
CoreM enhances this data by providing context, such as shift details, process order information, and SKU specifics. It aggregates and analyzes this information, detecting significant events and transforming them into actionable insights. By recording and analyzing all data, CoreM enables informed decision-making.
Furthermore, the recorded data can be stored in a data lake and combined with other enterprise data for advanced analytics such as AI and ML. This integration optimizes the entire enterprise, leading to enhanced efficiency and productivity.
Manufacturing Technology Integration with MES Software
Unlock the full potential of your manufacturing operations with CoreM’s seamless integration with your existing SCADA and Historian solutions. From customizable downtime tracking to IEE and product quality management, CoreM offers a comprehensive suite of features tailored to optimize your processes.
Our adaptable architecture ensures you can leverage your current investments by effortlessly integrating CoreM on top of your existing technologies. With CoreM’s intuitive low code development environment, you gain a unified view of your operations, streamlining processes, reducing manual effort, eliminating errors, and enhancing communication
and more!
MES Software Helps Manufacturer’s Find Losses, Improve Quality, and Reduce Costs
Boost Efficiency OEE
Improve efficiency by tracking and monitoring equipment effectiveness (OEE), downtime, waste, production counts, MTBF, MTTR, and more. Associate events with causes, analyze to identify root causes. Enhance standard OEE to deliver maximum results.
Greater Visibility Dashboards
Summarize and analyze data by context. Correlate events and reasons to production parameters. Use standard & ad-hoc reports and dashboards for real-time decisions. Our Manufacturing Intelligence solutions offer comprehensive visibility into the production process, providing detailed tracking and tracing capabilities for materials, products, and equipment, which can be crucial for regulatory compliance and effective supply chain management.
Reduce Waste
Minimize rework, errors, and waste by gaining better visibility into data quality and staying informed about recall information. Drive precision by visualizing, analyzing, optimizing, and executing with a closed-loop solution.
Improve Quality
Our MES solution improves product quality through real-time trends, statistics, and notifications. It integrates data from manual and automated sources, providing a single, centralized location for process, inspection, and test information. It also supports 21 CFR Part 11 compliance and allows for attaching operator comments, specifications, recipes, and procedure documents.
ERP Integration
ERP integration closes the information flow gap in real-time and transforms production by updating ERP orders, quality, and material usage. Any size manufacturing company can benefit from MES to ERP connectivity. We have provided real-time interfaces to SAP, Microsoft, Oracle and others.
Unify Your Data
We believe in working with a data modeling structure to unify your business data. The ISA-95 framework is a good reference for modeling by, Site, Area, Line, Cell to Edge. Once in place this Unified Namespace structure provides a powerful way to access data, structured and unstructured.
Data-Driven Decisions with MES Software
Harness The Power Of Manufacturing Intelligence with CoreM
Focus on optimizing manufacturing performance, improving efficiency, and reducing costs through data-driven insights and process improvements.
FEATURES
Agile Development
An agile MES Software Application that includes Downtime Monitoring and Data Entry.
FEATURES
Plant Model Configuration
Allows for the configuration of a plant model, organizing data and variables in a flexible ISA 95-like model.
FEATURES
Configurable Events
Includes configurable events for downtime events, waste, OEE calculations, quality management, batch events, reason code data entry, and user defined custom events.
FEATURES
Works With All Major Historians
An event historian application that integrates with process historians such as Canary Labs, OSISoft, GE Historian, InfluxDB, and Any SQL Historian.
FEATURES
SCADA Integration
The software integrates with Tatsoft’s FactoryStudio and Inductive Automation’s Ignition SCADA software to provide user interface screens and dashboards.
FEATURES
HTML5 Client
Includes an HTML5 client (RAS Application) with predefined displays that are configurable and can be customized in VisualStudio with ASP.NET.
FEATURES
Microsoft SQL Server Based
Based on Microsoft SQL Server and provides open and flexible reporting.
FEATURES
Data Access And Predefined Queries
Offers data access and many predefined queries and views for reporting key data and analysis.
FEATURES
ERP Integration
Interface with ERP Systems for a seamless flow of information between your systems.
An agile MES Software Application that includes Downtime Monitoring and Data Entry
Allows for the configuration of a plant model, organizing data and variables in a flexible ISA 95-like model.
Includes configurable events for downtime events, waste, OEE calculations, quality management, batch events, reason code data entry, and user defined custom events.
An event historian application that integrates with process historians such as Canary Labs, OSISoft, GE Historian, InfluxDB, and Any SQL Historian.
The software integrates with Tatsoft’s Factory Studio and Inductive Automation’s Ignition SCADA software to provide user interface screens and dashboards.
Includes an HTML5 client (RAS Application) with predefined displays that are configurable and can be customized in VisualStudio with ASP.NET
Based on Microsoft SQL Server and provides open and flexible reporting.
Offers data access and many predefined queries and views for reporting key data and analysis.
Interface with ERP Systems for a seamless flow of information between your systems.
MES SOFTWARE: Reduce downtime and monitor KPIs in a regulated environment
This company uses CoreM, our MES software, to reduce downtime, capture reason codes, and calculate KPIs including OEE.
- Secure Multi-Plant Enterprise System, local data collection (Edge), cloud/enterprise servers
- After extensive security screening INS3 CoreM passed this pharmaceutical companies security and Veracode testing
- FS Edge Gateway communicates to Rockwell and Custom controllers, acts as a Logic Engine to for real-time calculation and data processing
- SCADA and Web GUI and Dashboards communicate in real-time with CoreM SQL based MES Event Monitor
- Templated Asset types, Reason Codes, and Product descriptions for Rapid Deployment
- Trends and Display can interact directly with GE Historian for Time-Series Data Analytics
MES SOFTWARE: Real-time Production Monitor
Charter NextGen uses our MES software to monitor and present critical production parameters on 58 film lines
- Replace older difficult to maintain custom MES system
- Develop reusable Symbols and Screen Templates to deploy HTML5 Company, Plant, and Line overview displays.
- Dashboards communicate in real-time with machines, CoreM MES, manual input and ERP
- Custom machine driver written with Tatsoft driver toolkit
- Use of CoreM SQL based MES enabled efficient rollout to 58 lines across five locations
- Connection to Process Historian provides capability for detailed trend analysis on process events captured by CoreM
- Extensive use of dynamic visual templates. One line visual template that self-adjust based on how many layers of film
- DVR Functionality for playback and analysis of process events