Enhancing Productivity through Data Analysis for Manufacturing: Minimizing Down Time and Enhancing OEE
Blog
5 Min Read
Unplanned equipment downtime can be a major headache for manufacturers. It leads to higher costs, production delays, and, in some cases, the loss of a huge amount of revenue. So, to stay ahead of your competitors, you need a smarter way to track downtime and find its root causes even before they happen. And that’s where data analytics for manufacturing comes in.
By analyzing machine performance, your organization can move beyond traditional maintenance methods. For example, you can use machine learning in production to identify hidden issues, spot patterns, and even automate decision-making to minimize the risk of errors. This can help you predict failures before they happen and reduce downtime by a large margin.
However, before we start discussing data analytics for manufacturing, there’s something else we’d like to share for better understanding. Let’s begin.
Overall Equipment Effectiveness - A Brief Overview
OEE, in essence, is a method that helps you measure how well a manufacturing process is running. It focuses on three factors before making an assessment – availability, quality, & performance. The higher the OEE of your organization is, the more efficient the operation.
However, in order to improve your OEE, you’ll need real-time insights. And this can only be provided by machine data, sensors, and operational systems. By using data analytics for manufacturing, your organization can track downtime automatically, find what’s causing the issue, and predict failures before they happen.
You can learn more of OEE Efficiency at our blog manufacturing efficiency with OEE
Why Does OEE Matter in Manufacturing
With AI-driven manufacturing, organizations can detect failures early and fix them faster to prevent costly breakdowns. Apart from this, OEE can also help you with the following –
- When machines are working efficiently, their productivity will increase automatically. Your operators can adjust their workflows and settings to maximize their outputs.
- By identifying defects in real time, you can reduce waste and improve product consistency. Less downtime and higher efficiency can also help you bring in higher revenue.
Key Data Sources for Equipment Downtime Analysis
In order to lower downtime, you need to track both historical and real-time data. And by using the best AI-driven manufacturing system, you can pull information from different sources, including MES, SCADA, and ERP. So, first, let’s take a look at the type of data you should be focusing on –
Downtime Logs
Whether you’re logging it manually or automatically, this data includes various details like how long a machine was down, which equipment was affected, and initial information on what went wrong.
Categorized Downtime Events
In this case, you’ll have to classify different downtimes by its root cause, such as human error, mechanical failure, supply chain problems, or scheduled maintenance.
Maintenance Records
Keeping a record for both corrective and preventive maintenance is important. For this, you’ll need to include information or parts that were replaced during the maintenance & regular service history.
Production Schedules
Production goals, shift timings, and equipment usage data can provide context for when did the downtime occur (or when it might occur again) and why did it happen.
Operator Input and Micro-Downtimes
The machine operators of your organization will always spot problems first. So, their feedback on quality issues, minor stoppages, and recurring faults will be important for diagnostic inefficiencies.
MTBF and MTTR
MTBF (Mean Time Between Failures) usually measures how long a machine might run before failing. On the other hand, MTTR (Mean Time to Repair) tracks how quickly you can repair a tool or equipment after it breaks down.
OEE Metrics
OEE metrics are a combined measure of availability, quality, and performance that can help you assess the true impact of equipment downtime on productivity.
How to Perform a Data-Driven Analysis of Downtime
As a manufacturer, you’ll lose valuable time and money when machines stop working. However, data analytics for manufacturing can help them figure out why downtime happens and how you can fix it. By accumulating and analyzing data, you can make smarter decisions and cut expenses accordingly. Here’s how you can do it –
Record and Log Downtime Incidents
You can use an automated system and operator input to log downtime incidents properly. And once it’s done, then you’ll have to assign them to specific production lines, machines, and shifts for better tracking. Also, don’t forget to include reason codes to identify recurring issues quickly.
Review Downtime Causes and Duration
By using machine learning in production, you can group downtime events into the following categories –
- Mechanical Failures: Sensor malfunctions, motor breakdowns, or worn-out parts.
- Process Bottlenecks: Raw material shortages, slow workflows, and affected tools.
- Preventive vs. Corrective Maintenance: Planned service & last-minute emergency repairs.
- Human Error: Operator mistakes, incorrect machine settings, or miscommunication.
Before you begin working on fixing it, it’s always important to identify which downtime event is happening the most. You can, then, categorize it by shift, product, or machine
Calculate MTTR and MTBF
MTBF is all about showcasing the total operating time and dividing it by the number of failures that occurred in the machine. On the other hand, MTTR can be determined by dividing total repair time with the number of repairs in equipment. With AI-powered analysis, you can identify the patterns in MTBF data and predict failures earlier than usual.
Conduct Root Cause Analysis Using AI and Machine Learning
Instead of fixing the same issues again and again, you can also use data analytics for manufacturing to dig deeper. Here are some tools you can choose from –
- AI-powered Whys Analysis: It works by asking “why” multiple times to identify the issue.
- Fishbone (Ishikawa) Diagrams: These are AI-generated cause-&-effect models, which can be used to get better insights about a problem.
- Pareto Analysis (80/20 Rule): With this, you can focus on the small number of causes responsible for most downtime and fix them one-by-one.
Measure the Impact of Downtime on OEE
Downtime directly decreases OEE (overall equipment effectiveness) by reducing equipment availability. So, you can use machine learning in production to measure OEE losses in ral-time and run a ‘what-if’ scenario to test for different solutions.
Implement AI-Powered Corrective Actions
By applying manufacturing data, your organization can –
- Schedule maintenance at the right moment to prevent failure
- Use different machine learning algorithms to predict when repairs are required
- Train your operators to reduce human errors and prevent unnecessary stoppages
Keep on Monitoring
Remember, fixing downtime issues isn’t really a one-time task anymore. Continuous monitoring with data analytics for manufacturing ensures –
- Tracking downtime trends in real-time
- Getting alerts when downtime exceeds the limits you have set
- Benchmarking against industry standards to stay competitive
How INS3 Converts Downtime Findings into Practical Outcomes?
INS3 brings a complete range of engineering services and software solutions to help manufacturers. From machine data collection to automated downtime analysis, our team helps businesses shift from fixing regular issues to preventing them before they actually happen.
By implementing machine learning in production, AI-driven insights, and data analytics for manufacturing, we can help manufacturers with –
Predict Downtime before It Happens
We integrate AI solutions that spot early warning signs to allow manufacturers to take action before a breakdown occurs. By using machine learning in production, your company won’t just react – it’ll stay ahead of failures and make sure that the operations are going smoothly.
Track Downtime in Real Time
Our solutions directly connect with SCADA, PLC, MES, and ERP systems to eliminate human error in data collection. This will help you get accurate, real-time insights to make better decisions.
Boost OEE and Cut Costs
Companies that are using real-time data analytics for manufacturing and predictive analysis have achieved the following –
- 15-30% reduction in unplanned downtime
- Lower costs through optimized preventive maintenance
- 10-20% increase in production rates
Improving your business’s productivity while ensuring reduced downtime is a difficult task to manage – no matter how proficient you are. That’s why it’s always better to delegate a few things to someone with proper expertise in this matter, like INS3.
So, are you ready to take your manufacturing business to the next level? Let’s get connected.
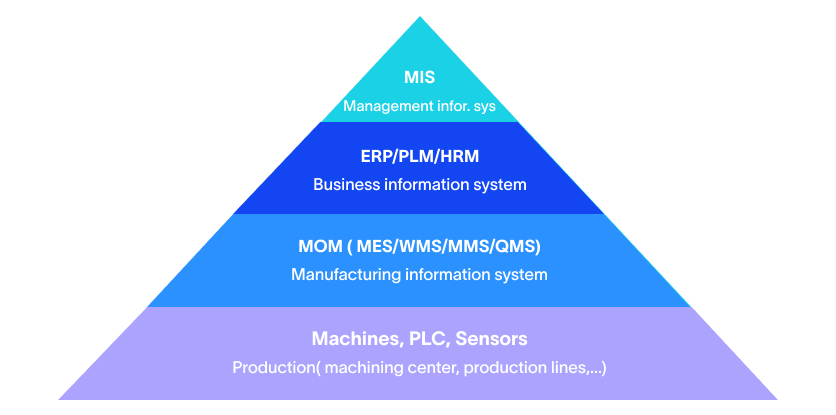
Agile MES: The Key to Unlocking Smart Manufacturing Success
MES is a computerized system used in manufacturing operations to track and document the transformation of raw materials into finished goods. An MES system typically manages and monitors work orders, equipment, materials, and personnel on the shop floor. The system provides real-time visibility into production processes, helps optimize manufacturing operations, and improves the overall efficiency of the manufacturing process.
Understanding OEE: The Key to Manufacturing Efficiency
In today’s competitive manufacturing landscape, improving efficiency and productivity is crucial for businesses to remain competitive. One of the key metrics used to measure manufacturing efficiency is OEE or Overall Equipment Effectiveness. In this blog, we will take a closer look at OEE and its importance in manufacturing.
How to Effectively Conduct a Legacy System Integration
Legacy system integration can be a daunting task, but it’s a necessary one for many manufacturers that rely on outdated systems to run their business. Integrating legacy systems with modern technology can improve efficiency, streamline processes, and save time and money. However, it’s important to approach the integration process carefully and methodically to ensure success.
Share on :
Keep On Reading
Subscribe to Our Newsletter
Subscribe to our weekly newsletters to get updates regarding our new production, behind the scene process of our art creation and much more.
After submitting this form you will receive an e-mail with a confirmation link that you must click to complete your request. Detailed information on processing and cancellation can be found in our privacy policy.