Extend Ignition with MES Software for Manufacturing Intelligence
Blog
4 Min Read
In the current world of manufacturing, the use of data in decision making has become a key factor in competitiveness. Although Ignition SCADA provides effective tools for monitoring and controlling processes on the shop floor, manufacturers require much more than SCADA to remain competitive—they require an MES solution that will enable real-time management of the production process, obtain critical metrics, and facilitate ongoing improvement. Integration of Ignition with SQL-based MES software opens a new level of operational visibility, which allows businesses to solve such important problems as production, downtime, and quality.
At its core, Ignition provides real-time monitoring and control over manufacturing processes. However, this SCADA functionality focuses mainly on machine-level data. By integrating Ignition with SQL-based MES software, manufacturers can leverage their SCADA data to address broader business challenges and gain more valuable insights into their operations. Here’s how SQL-based MES software can extend Ignition and resolve common business issues:
Ignition MES: Why Extend Ignition with MES Software
Improved Production Visibility
While SCADA systems such as Ignition perform well at capturing real-time information from machines and processes, this information remains isolated in the control system. With the help of MES software, companies can accumulate data, making production performance information unified. This allows operators, managers and decision makers to have a complete picture of the production process, hence improving the overall management of the process.
Real-Time Downtime and OEE Tracking
SQL-based MES software complements Ignition’s monitoring capabilities by automatically capturing machine-level events like downtime and using this data to calculate Overall Equipment Effectiveness (OEE). OEE is one of the most important metrics to determine the efficiency of production and if an MES is not present then it becomes cumbersome to track and analyze it. MES software is capable of documenting reasons why and real-time calculation of efficiency and performance. This enables the manufacturers to concentrate on minimizing the avoidable downtime, enhancing the first-pass yield and in the long run enhancing output and profitability.
Better Quality Control and Traceability
One of the key business challenges manufacturers face is maintaining consistent product quality. Ignition provides information about the performance of the machines, but with an SQL-based MES, manufacturers can implement quality control into the production line. MES systems can record defects, monitor the quality, and provide traceability from one line to another. This integration also allows manufacturers to easily comply with industry regulations and customer standards while minimizing rework and waste.
ERP Integration for Real-Time Data Flow
Ignition by itself can monitor production data but when combined with SQL-based MES software enables real-time data exchange between the shop floor and Enterprise Resource Planning (ERP) systems. This ensures that production data—such as material usage, order confirmations, and batch tracking—flows seamlessly to ERP systems, allowing for accurate inventory management and order processing. Real-time updates reduce errors, eliminate manual data entry, and provide visibility into how production aligns with broader business goals.
Enhanced Production Scheduling and Resource Utilization
Real-time machine data from Ignition can be integrated into planning systems making SQL-based MES software helpful in enhancing production scheduling. This leads to optimized schedules that account for machine availability, resource constraints, and demand fluctuations. It enables manufacturers to better manage the resources required in production, minimize bottlenecks, and increase throughput while improving resource utilization.
Addressing Key Business Issues with MES Software
By extending Ignition’s capabilities with SQL-based MES software, manufacturers can resolve several key business challenges, including:
- Downtime Reduction: MES tracks and analyzes downtime events in real-time and helps reduce unplanned stops and maximizes equipment utilization.
- Production Efficiency: OEE tracking provides a clear understanding of production performance, enabling targeted improvements in efficiency.
- Cost Control: MES helps manufacturers reduce waste and production costs by improving visibility, quality control, and resource management.
- Regulatory Compliance: Integrated quality tracking and traceability ensure that manufacturers can meet stringent regulatory and customer standards.
Why CoreM from INS3? The best MES Software for Ignition
If you’re considering extending Ignition SCADA with an SQL-based MES, CoreM from INS3 is a powerful option. CoreM works with Ignition and adds real-time OEE, downtime event capture with reason codes, quality tracking, and ERP integration to it. INS3’s expertise in MES and Ignition implementations ensures that CoreM works with your existing Ignition SCADA system to offer a complete solution for making data driven decisions tailored to your operational needs.
Moreover, INS3 is Ignition Gold Certified, which means their team brings deep knowledge of Ignition and a proven track record of delivering results. When you choose INS3’s MES software and work with our Ignition specialists, you are not only getting a product, but a team that knows how to optimize Ignition for greater operational efficiency.
INS3 has developed a proven process that consistently gets results for manufacturers using Ignition. Whether you’re looking to improve efficiency, reduce downtime, enhance quality management, or improve your SCADA system, INS3’s combination of MES knowledge and Ignition expertise can drive meaningful improvements in your manufacturing operation.
By choosing CoreM and INS3, manufacturers gain a scalable, flexible, and highly integrative solution to meet their MES needs, all while taking advantage of the robust SCADA capabilities Ignition, GE, Rockwell, Tatsoft, or Aveva Wonderware offers.
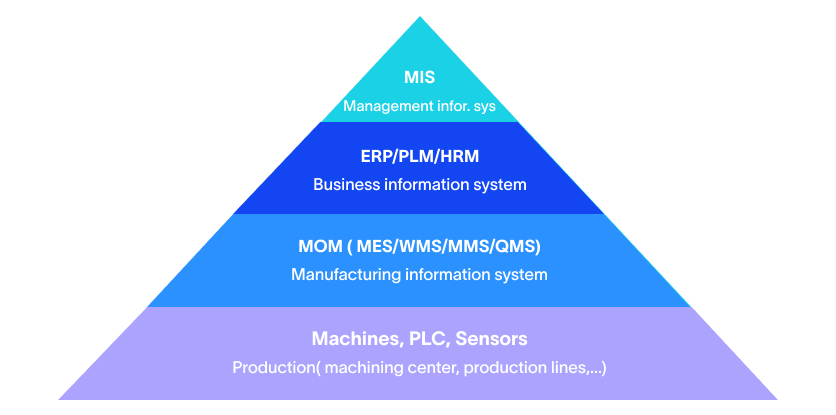
Agile MES: The Key to Unlocking Smart Manufacturing Success
MES is a computerized system used in manufacturing operations to track and document the transformation of raw materials into finished goods. An MES system typically manages and monitors work orders, equipment, materials, and personnel on the shop floor. The system provides real-time visibility into production processes, helps optimize manufacturing operations, and improves the overall efficiency of the manufacturing process.
Understanding OEE: The Key to Manufacturing Efficiency
In today’s competitive manufacturing landscape, improving efficiency and productivity is crucial for businesses to remain competitive. One of the key metrics used to measure manufacturing efficiency is OEE or Overall Equipment Effectiveness. In this blog, we will take a closer look at OEE and its importance in manufacturing.
How to Effectively Conduct a Legacy System Integration
Legacy system integration can be a daunting task, but it’s a necessary one for many manufacturers that rely on outdated systems to run their business. Integrating legacy systems with modern technology can improve efficiency, streamline processes, and save time and money. However, it’s important to approach the integration process carefully and methodically to ensure success.
Share on :
Keep On Reading
Subscribe to Our Newsletter
Subscribe to our weekly newsletters to get updates regarding our new production, behind the scene process of our art creation and much more.
After submitting this form you will receive an e-mail with a confirmation link that you must click to complete your request. Detailed information on processing and cancellation can be found in our privacy policy.