Stop Drowning in Manufacturing Data—Start Making Better Decisions
Blog
3 Min 58 Sec Read
Implementing manufacturing data analytics solutions can lead to redundancy. Manufacturers often drown themselves in manufacturing data, especially when they don’t ask the right questions while collecting data.
The first and most important question here is: Are you collecting the right data you need for decision-making?
Most manufacturers collect massive amounts of operational data but struggle with factory visibility because they’re gathering information without understanding what they need to know. The real challenge isn’t real-time data vs. static reports—it’s ensuring your data collection strategy provides context for informed decisions.
This ERP disconnect happens when manufacturers collect data in isolation instead of building integrated architectures. The integrated architecture combines time-series historian data with manufacturing event-driven systems. Success requires Unified Namespace architectures that collect the right data with proper context for manufacturing data analytics for business results.
Want to dive deeper into data-driven transformation? Explore our guide on how manufacturing data analytics boosts real-time decision-making and operational efficiency.
What Data Are You Really Collecting?
OT data analytics starts with understanding exactly what information your systems capture and whether it provides the context needed for effective decision-making.
Most manufacturing facilities collect two distinct types of operational data:
Time-Series Process Data
This type of data flows continuously from SCADA systems—temperatures, pressures, flow rates, energy consumption, vibration levels. This creates detailed operational timelines but often lacks the manufacturing context needed to understand the data; especially the meaning of the data for business performance.
Manufacturing Event Data
This type of Data captures discrete occurrences—batch completions, quality test results, equipment alarms, maintenance activities, and operator interventions. These events provide context but typically exist in separate systems from the process of data that explains why they occurred.
The critical question isn’t whether you’re collecting enough data, but whether your data collection strategy provides context for decision-making:
- Can you correlate quality failures with the process conditions that caused them?
- Do you understand which equipment performance patterns predict maintenance needs?
- Can you connect energy consumption spikes to specific production activities?
Without integrated historian architectures that combine time-series and event data, real-time production insights remain fragmented across systems that can’t communicate effectively.
Want to unlock even more value from your production data? Discover how the right manufacturing data analytics tools can supercharge your MES system’s impact.
The Context Problem: Why ERP Isn't Enough
ERP reporting limitations become obvious when manufacturers try to use transactional systems for business analytics in the manufacturing industry for applications that require operational context.
Static data vs. real-time decisions represents a fundamental mismatch. ERP systems excel at recording what happened but provide little insight into why and the ways to prevent similar issues.
Consider what happens when you lack integrated context:
A quality failure appears in your ERP system as a cost variance, but you can’t connect it to the process conditions during production, maintenance activities that preceded it, or operator decisions that may have contributed. Without this context, you’re managing symptoms rather than addressing root causes.
Manufacturing data analytics requires historian integration that combines continuous process monitoring with discrete manufacturing events within unified architectures that provide complete operational context for business decisions.
Curious how data at the edge transforms real-time decisions on the factory floor? Dive deeper into our guide on manufacturing data analytics.
Building Integrated Data Architecture
Manufacturing decision support systems achieve breakthrough performance when they integrate time-series historian data with manufacturing event-driven systems within Unified Namespace architectures.
Comprehensive Data Integration through OT/IT integration creates complete operational pictures. Once equipment performance degrades, operators see both the process trends leading to the issue and the manufacturing events that contributed to the problem.
Contextualized Analytics enable manufacturing process optimization by connecting time-series process data with manufacturing events and business context:
- Quality deviations link directly to process conditions, production parameters, and operator actions.
- Equipment failure predictions combine vibration trends, maintenance history, and production schedules.
- Energy optimization correlates consumption patterns with production activities and process requirements.
The key advantage lies in creating unified data architectures where time-series process data and manufacturing events exist within the same analytical framework, enabling contextualized insights that neither data type could provide independently.
Explore how real-time manufacturing data can transform operations—read our guide on implementing effective manufacturing data analytics strategies.
How INS3 Delivers the Right Data Architecture
Manufacturing data analytics success requires a strategic assessment of what data you’re collecting and building integrated historian architectures that provide proper context for decision-making.
Discovery: Understanding Your Current Data
INS3 takes a segmented approach to understanding the data you collect. First, it evaluates the data you collect. Then it analyzes whether the data supports effective decision-making or not:
Data Collection Assessment: We evaluate your time-series historians, manufacturing execution systems, and SCADA platforms to understand what information you’re capturing and where context gaps exist.
Decision-Making Analysis: Our team identifies critical decisions your operations teams need to make, then maps whether your current data collection provides the context needed to make those decisions effectively.
Phased Implementation Strategy
Instead of disruptive system replacements, INS3 takes an integrated historian architecture through proven phases. Here are the three phases of implementation:
Phase 1 – Data Foundation: Establish the data you need for specific decisions. After that, you’re ready to implement secure collection and basic correlation capabilities that showcase immediate value.
Phase 2 – Context Integration: Deploy the Unified Namespace architecture that integrates time-series and event data, enabling contextualized insights across operational and business systems.
Phase 3 – Advanced Analytics: Implement predictive capabilities that leverage integrated historian data to turn manufacturing data into business decisions.
Ongoing Optimization
INS3 ensures your data architecture continues supporting effective decision-making through performance monitoring, system evolution, and knowledge transfer that builds internal capabilities.
Want to explore more ways data is transforming factories? Check out our deep dive on Manufacturing Data Analytics to unlock smarter insights.
Results: From Data to Decisions
Integrated historian architectures deliver measurable outcomes through manufacturing data analytics that combine the right data with proper context.
Manufacturers gain enhanced root cause analysis capabilities by correlating process conditions with manufacturing events and business outcomes. Predictive insights from integrated data enable maintenance strategies that optimize equipment reliability while minimizing disruption.
Quality optimization becomes possible through real-time correlation between process parameters and manufacturing events, enabling proactive management that prevents defects. Financial impact comes through improved equipment utilization, reduced unplanned downtime, enhanced product quality, and optimized resource consumption.
Explore our complete guide on manufacturing data analytics and take your decision-making to the next level.
Start with the Right Questions!
The first step toward using manufacturing data analytics is to use the right data. Digital transformation in manufacturing becomes successful when manufacturers understand the data they are collecting first. Next, they must consider whether the data provides any context for making an effective decision.
In manufacturing, business intelligence requires integrated historian architectures combining time-series process data with manufacturing events and business context. The path ahead starts with asking the right questions about the decisions you must make. Next, it comes down to building Unified Namespace architectures that collect and integrate information necessary for effective decision making.
Ultimately, success isn’t about collecting more information – it’s about collecting data with a proper context, next integrating that information inside the unified architecture that enables better decisions to come through. Eventually, the right decisions translate into desired business results.
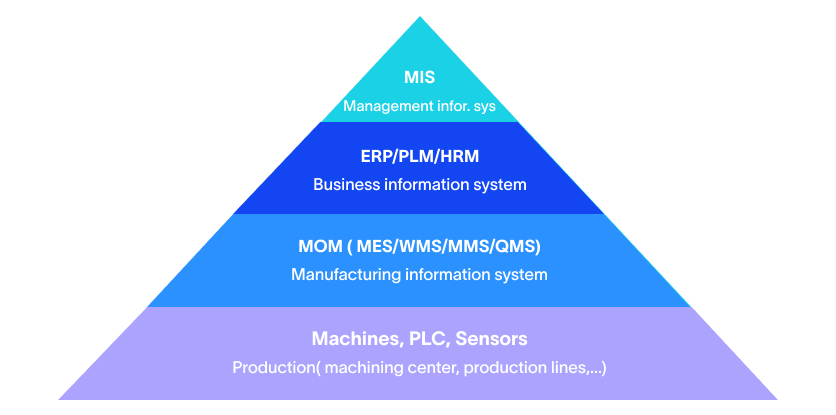
Agile MES: The Key to Unlocking Smart Manufacturing Success
MES is a computerized system used in manufacturing operations to track and document the transformation of raw materials into finished goods. An MES system typically manages and monitors work orders, equipment, materials, and personnel on the shop floor. The system provides real-time visibility into production processes, helps optimize manufacturing operations, and improves the overall efficiency of the manufacturing process.
Understanding OEE: The Key to Manufacturing Efficiency
In today’s competitive manufacturing landscape, improving efficiency and productivity is crucial for businesses to remain competitive. One of the key metrics used to measure manufacturing efficiency is OEE or Overall Equipment Effectiveness. In this blog, we will take a closer look at OEE and its importance in manufacturing.
How to Effectively Conduct a Legacy System Integration
Legacy system integration can be a daunting task, but it’s a necessary one for many manufacturers that rely on outdated systems to run their business. Integrating legacy systems with modern technology can improve efficiency, streamline processes, and save time and money. However, it’s important to approach the integration process carefully and methodically to ensure success.
Share on :
Keep On Reading
Subscribe to Our Newsletter
Subscribe to our weekly newsletters to get updates regarding our new production, behind the scene process of our art creation and much more.
After submitting this form you will receive an e-mail with a confirmation link that you must click to complete your request. Detailed information on processing and cancellation can be found in our privacy policy.