The OEE Illusion — Why Tracking Isn't Improving Performance
Blog
5 Min 31 Sec Read
Most manufacturers discover a sobering reality when they implement OEE software solutions: their actual equipment effectiveness often averages around 45-60%, significantly lower than what operations teams believe possible.
Yet installing OEE tracking software often fails to move these numbers meaningfully upward.
The fundamental issue isn’t the measurement itself—it’s the disconnect between tracking and action. Traditional manufacturing KPI improvement approaches focus on collecting data rather than empowering operators to use that information for real-time performance enhancement.
Effective OEE improvement requires more than software. It demands integrated systems that combine real-time machine data collection with operator input, intuitive interfaces that drive immediate action, and comprehensive training that enables sustainable results.
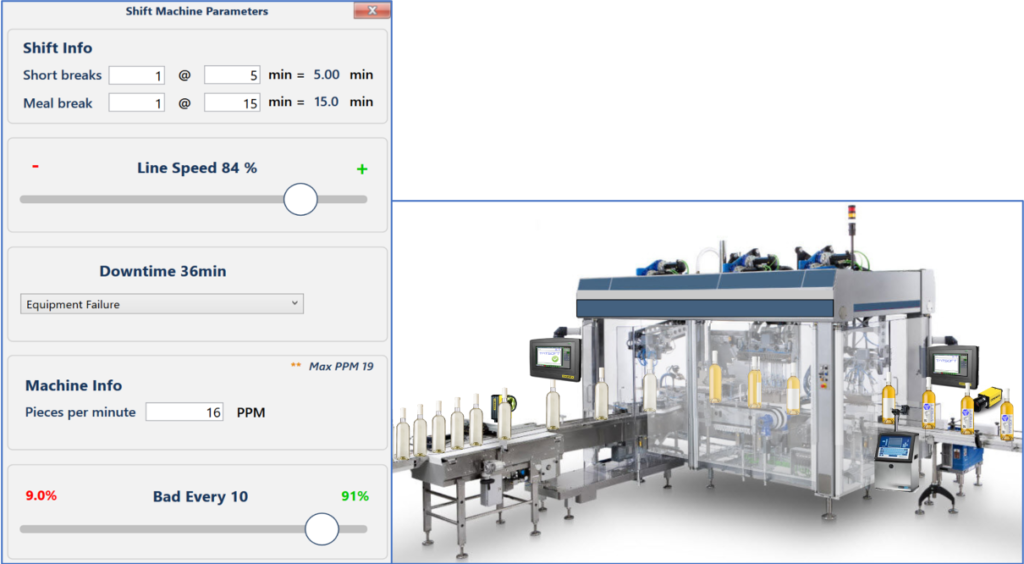
The Tracking Trap: Why OEE Numbers Don't Move
OEE software solutions implementations frequently disappoint because they measure without enabling improvement. Production efficiency metrics remain static when operators can’t connect their actions to the numbers they see.
Consider the typical scenario: Manufacturing teams install OEE monitoring software systems that calculate availability, Performance, and quality metrics from historical data. Reports show efficiency trends, but operators lack the real-time information and contextual understanding needed to influence those trends.
Common tracking limitations include:
- Delayed reporting that shows problems hours or days after they occur
- Limited context that fails to explain why efficiency dropped
- Operator disconnection from the data collection and improvement process
- Missing root cause information that prevents sustainable problem resolution
The 45-60% baseline reality becomes particularly frustrating when tracking systems highlight the problem without providing operators with the tools and training needed to address underlying causes.
Real improvement requires moving beyond passive measurement to active operator engagement with real-time data systems that enable immediate response to efficiency challenges.
Want to see how OEE software solutions can deliver real ROI? Learn how integrating expert systems can transform your manufacturing efficiency
Real-Time Data Collection and Operator Input
Effective OEE software solutions must capture both automatic machine data and operator knowledge to create complete operational pictures that drive improvement.
Real-Time Machine Data Collection provides the foundation for responsive OEE systems. Modern manufacturing equipment generates continuous streams of operational data—cycle times, speeds, temperatures, pressures—that reveal equipment performance patterns as they occur.
Operator Input Integration adds the human context that machines cannot provide:
- Downtime reason codes that explain why the equipment stopped
- Waste reason codes that categorize quality issues and material losses
- Production confirmations that verify completion of batches or jobs
- Process adjustments that document operator interventions and their results
Root cause analysis becomes possible when real-time machine data combines with operator input to create comprehensive event timelines. When efficiency drops, operators can immediately see both the technical conditions that contributed to the issue and the contextual factors that may have influenced Performance.
The best OEE software solutions integrate these data sources seamlessly, ensuring operators can focus on improvement rather than data entry complexity.
Read our guide on Unlocking Manufacturing Efficiency with OEE to discover how to turn insights into action and drive real results on the factory floor.
Operator-Centric Systems: Dashboards That Drive Action
Manufacturing KPI improvement accelerates when operators have access to intuitive interfaces that translate complex data into actionable insights.
Operator-Centric Dashboard Design prioritizes usability over sophistication. The dashboard drives action in multiple ways. It has clear visual indicators, making it easy for users to check OEE status at a glance.
OEE software solutions with an operation-centric dashboard let users stay on track with performance graphs. If the production performance drops by a small margin, immediate alerts on a user-friendly dashboard help identify that instantly.
Operators can use the trend display to understand the patterns in the production process and predict issues that need attention. Additionally, Operator-Centric Systems OEE software solutions include action prompts. These prompts guide the operators throughout the process.
Real-Time Alerts and Notifications enable proactive rather than reactive management. When equipment efficiency begins declining, operators receive immediate notification with contextual information about potential causes and recommended actions.
Intuitive Data Entry systems make operator input effortless. Touch-screen interfaces with pre-configured reason codes, visual selection tools, and voice input capabilities ensure data collection doesn’t interrupt production flow.
The goal is to create systems where operators naturally engage with OEE data because the interfaces support their workflow rather than complicating it.
Read our guide on Understanding OEE: The Key to Manufacturing Efficiency to master the metrics that matter most.
Maximizing OEE Through Operator Development
OEE education programs that combine operational understanding with system proficiency amplify technology investments significantly.
Fundamental OEE Concepts training ensures operators understand how their actions influence efficiency metrics:
- The Six Big Losses that impact equipment effectiveness
- Availability, Performance, and Quality relationships and how operator decisions affect each component
- Root cause thinking that moves beyond symptoms to address underlying issues
- A continuous improvement mindset that makes efficiency optimization an ongoing priority
Operators are able to use the OEE software solutions more effectively through operator development training. System Operation Training builds proficiency with real-time data tools.
The training enables operators to use dashboard interpretations and know what the numbers mean. The alert responses guide the right and appropriate actions for different scenarios. Additionally, the data input practices ensure accurate reasons for code selection and production confirmations. Operators also learn to troubleshoot common system issues without additional help.
Sustainable Improvement Programs create cultures where OEE scores improve; manufacturing becomes an integral part of daily operations rather than a special initiative.
From Data to Decisions: Real OEE ROI
OEE ROI materializes when real-time data systems enable operators to make immediate improvements that accumulate into measurable business outcomes.
Reduced Downtime results from faster problem identification and response. When operators receive immediate notification of efficiency degradation with contextual information about potential causes, they can address issues before they escalate into significant losses.
Improved Throughput emerges through continuous optimization. Real-time performance feedback enables operators to fine-tune processes, identify optimal operating parameters, and maintain peak efficiency consistently.
Enhanced Quality develops through immediate visibility into quality trends and their relationship to process parameters. Operators can adjust conditions proactively to prevent defects rather than detecting quality issues after production.
Operational Cost Reduction occurs through:
- Waste minimization enabled by real-time material usage tracking
- Energy optimization through immediate visibility into consumption patterns
- Maintenance efficiency is driven by predictive indicators that optimize timing
- Labor productivity improvements through better task prioritization and resource allocation
Measurable efficiency gains typically compound over time as operators become more proficient with real-time data systems and develop a deeper understanding of equipment performance patterns.
Read our blog The OEE Illusion — Why Tracking Isn’t Improving Performance to uncover how to move from data collection to real improvement.
The INS3 Difference: Integrated Real-Time OEE Software Solutions
Smart OEE strategy requires more than software implementation—it demands comprehensive approaches that integrate technology, training, and ongoing optimization within proven methodologies.
Customized KPI Frameworks
INS3 makes a difference for manufacturers who want to experience a real improvement in their equipment and manufacturing process. The first step to that starts with a customized KPI framework that adapts standard OEE metrics to specific operational requirements.
It relies on Industry-specific efficiency indicators that reflect unique production challenges. In addition, it includes Industry-specific efficiency indicators that reflect unique production challenges, helping track metrics that matter.
The Equipment-tailored performance metrics also contribute to the KPI frameworks that operators can customize. Therefore, it’s easier to evaluate the efficiency of different machinery.
Ultimately, the quality measures and cost integration aligned with specific customer, regulatory, and financial requirements make INS3 the perfect choice for manufacturers.
Operator-Centric Implementation
There’s no point in implementing OEE software solutions if the learning curve and day-to-day use case of the solution are steep and difficult.
OEE solution providers must ensure that the technology serves operational teams effectively. That’s what INS3 is good at. It allows user interface customization that matches operator workflows and skill levels. They include training programs that build both OEE understanding and system proficiency.
Furthermore, they have a phased deployment that allows operators to master capabilities progressively. Ongoing support that maintains system effectiveness and user engagement also makes OEE implementation a lot easier.
Proven Results Methodology
INS3 OEE solutions focus on outcome through a simplified OEE software solutions implementation process. They deliver measurable results through a baseline assessment that establishes current Performance accurately. Their gap analysis identifies the highest-impact improvement opportunities, allowing operators to see what needs improvement.
Additionally, the systematic implementation process minimizes disruption while maximizing adoption. Their performance monitoring ensures sustained improvement and identifies optimization opportunities.
Contextual Manufacturing Analytics
Finally, INS3’s OEE software solutions combine real-time machine data, operator input, and business intelligence to create comprehensive operational visibility that drives both immediate improvements and strategic decision-making.
Conclusion: From Measurement to Mastery
Manufacturing performance transformation occurs when OEE systems move beyond tracking to enable operator-driven improvement through real-time data, intuitive interfaces, and comprehensive training.
Contextual manufacturing analytics succeed when they combine automatic data collection with operator knowledge, creating complete operational pictures that support both immediate problem-solving and long-term optimization strategies.
The path forward requires integrated approaches that treat OEE as an operator empowerment tool rather than just a measurement system. When operators understand efficient drivers, have access to real-time performance data, and possess the training needed to take effective action, OEE improvement becomes sustainable and scalable.
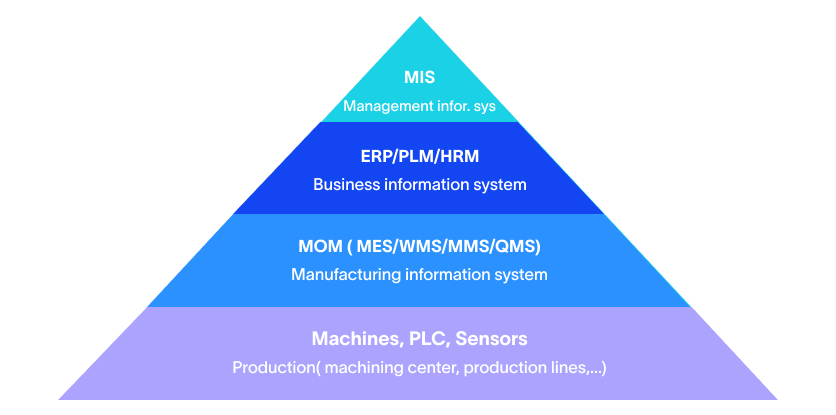
Agile MES: The Key to Unlocking Smart Manufacturing Success
MES is a computerized system used in manufacturing operations to track and document the transformation of raw materials into finished goods. An MES system typically manages and monitors work orders, equipment, materials, and personnel on the shop floor. The system provides real-time visibility into production processes, helps optimize manufacturing operations, and improves the overall efficiency of the manufacturing process.
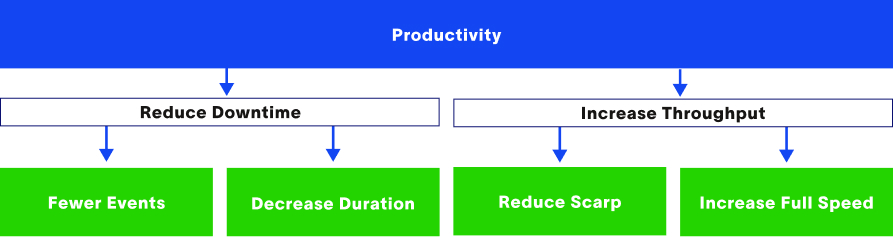
Understanding OEE: The Key to Manufacturing Efficiency
In today’s competitive manufacturing landscape, improving efficiency and productivity is crucial for businesses to remain competitive. One of the key metrics used to measure manufacturing efficiency is OEE or Overall Equipment Effectiveness. In this blog, we will take a closer look at OEE and its importance in manufacturing.
How to Effectively Conduct a Legacy System Integration
Legacy system integration can be a daunting task, but it’s a necessary one for many manufacturers that rely on outdated systems to run their business. Integrating legacy systems with modern technology can improve efficiency, streamline processes, and save time and money. However, it’s important to approach the integration process carefully and methodically to ensure success.
Share on :
Keep On Reading
Subscribe to Our Newsletter
Subscribe to our weekly newsletters to get updates regarding our new production, behind the scene process of our art creation and much more.
After submitting this form you will receive an e-mail with a confirmation link that you must click to complete your request. Detailed information on processing and cancellation can be found in our privacy policy.