What is MES and how it can help your business.
Blog
4 Min Read
The manufacturing industry has undergone a significant evolution over the past several decades, driven by advances in technology, globalization, and changing customer demands. In the early days of manufacturing, production was largely manual and labor-intensive, with workers using basic tools and equipment to produce goods. This gave way to mass production techniques in the mid-20th century, which enabled manufacturers to produce goods on a larger scale and at a lower cost, thanks to the use of assembly lines and standardized parts.
With the advent of computers and automation in the 1970s and 1980s, manufacturers began to adopt new technologies to further optimize their production processes. Computer-controlled machines and robots enabled manufacturers to produce goods more efficiently and accurately, while computer-aided design (CAD) and computer-aided manufacturing (CAM) software improved the design and production of complex products.
More recently, the rise of smart manufacturing has brought new technologies such as the Industrial Internet of Things (IIoT), Manufacturing Intelligence (MI), and Big Data Analytics to the factory floor. These technologies enable manufacturers to collect and analyze data in real-time, providing insights into production processes and enabling them to make better decisions.
Today, the manufacturing industry continues to evolve, with manufacturers embracing new technologies to improve efficiency, reduce costs, and respond to changing customer demands. This shift towards smart manufacturing is driven by a combination of factors, including advances in technology, increasing competition, and changing customer demands.
By integrating data from across the production process, smart manufacturing enables manufacturers to make better decisions, improve quality, and reduce waste. With the ability to monitor production processes in real-time, manufacturers can respond more quickly to changes in demand and optimize their production processes accordingly.
What is MES?
Manufacturing Execution Systems (MES) are computerized systems designed to manage and monitor production processes on the shop floor. It provides real-time information about production activities, equipment status, and product quality, allowing manufacturers to optimize their operations and make informed decisions. In this blog, we’ll take a closer look at MES, what it is, and how it can help your business.
MES is designed to connect the shop floor with the rest of the organization by integrating with other enterprise systems such as Enterprise Resource Planning (ERP), Product Lifecycle Management (PLM) and Supply Chain Management (SCM) systems. Hence, MES can help manufacturers manage, monitor and control manufacturing processes on the shop floor.
MES provides real-time visibility into production processes and helps manufacturers improve operational efficiency, reduce costs, and increase productivity. It captures data from various sources such as machines, sensors, and workers, and provides insights into the manufacturing process. MES can also automate and streamline manual processes, reducing errors and improving data accuracy. MES typically includes modules for production scheduling, resource allocation, quality management, maintenance management, and data collection and analysis. It can also integrate with other systems such as barcode scanners, RFID readers, and other automation systems to streamline the manufacturing process.
MES typically includes modules for:
- Production scheduling and planning
Production scheduling and planning is an important module of an MES (Manufacturing Execution System) that enables manufacturers to manage their production operations more effectively. This module allows manufacturers to create production schedules that take into account resource availability, delivery schedules, and customer demands. With production scheduling and planning, manufacturers can allocate resources such as labor, materials, and equipment to specific production runs, ensuring that all resources are utilized efficiently and effectively. - Workforce management:
This module provides real-time visibility into employee schedules, attendance, and productivity, enabling manufacturers to optimize their workforce utilization and ensure that all tasks are completed on time. - Quality management
With MES, manufacturers can track production data in real-time, monitor equipment performance, and perform inspections to identify defects and ensure that products meet required quality standards. - Inventory management
With MES invetory, manufacturers can track raw materials, work in progress (WIP), and finished goods in real-time, enabling them to optimize their inventory levels, reduce waste, and improve resource utilization. - Equipment maintenance
With MES, manufacturers can track their equipment, including maintenance schedules, perform preventive maintenance, and identify breakdowns in real-time, enabling them to minimize equipment downtime, reduce maintenance costs, and improve equipment reliability.
Why does your business need an MES?
Manufacturing companies need an MES (Manufacturing Execution System) to optimize their production processes, increase productivity, and improve product quality. MES provides real-time visibility into production operations, allowing manufacturers to monitor their production processes, identify bottlenecks, and optimize resource utilization. With MES, manufacturers can automate manual processes, reduce waste, and improve workflow, leading to increased efficiency and productivity. MES also helps manufacturers improve product quality by providing real-time monitoring and inspection of production processes, identifying defects, and implementing corrective actions. Furthermore, MES can help manufacturers comply with regulatory requirements by providing real-time data on production processes, product quality, and equipment maintenance. By leveraging an MES, manufacturers can improve their operations, reduce costs, and make better-informed decisions. MES is an essential tool for manufacturers seeking to remain competitive in an increasingly complex and dynamic business environment.
MES can provide many benefits to manufacturers, including:
- Improved productivity
One of the primary benefits of an MES (Manufacturing Execution System) is improved productivity. By providing real-time visibility into production processes, MES can help manufacturers identify bottlenecks, reduce downtime, and optimize resource utilization.With MES, manufacturers can monitor production processes in real-time, enabling them to identify and address bottlenecks as they occur. This helps manufacturers optimize production processes, minimize production delays, and improve overall efficiency.
- Increased efficiency
Another significant benefit of an MES (Manufacturing Execution System) is increased efficiency. MES can help manufacturers optimize their operations by automating manual processes, reducing waste, and improving workflow. By automating manual processes such as data entry and documentation, MES can help manufacturers reduce errors and improve overall efficiency. This can be particularly valuable in highly regulated industries such as pharmaceuticals, where accuracy and compliance are critical. - Enhanced quality
MES can help manufacturers optimize their operations by automating manual processes, reducing waste, and improving workflow.
By automating manual processes such as data entry and documentation, MES can help manufacturers reduce errors and improve overall efficiency. This can be particularly valuable in highly regulated industries such as pharmaceuticals, where accuracy and compliance are critical. - Better decision-making
MES can help manufacturers make informed decisions by providing real-time data on production processes, equipment status, and product quality. By collecting and analyzing data from various sources such as machines, sensors, and human input, MES can provide manufacturers with real-time insights into production processes. This enables manufacturers to identify bottlenecks, track performance, and optimize production processes. - Regulatory compliance
MES can help manufacturers comply with regulatory requirements by providing real-time data on production processes, product quality, and equipment maintenance.
In the manufacturing industry, compliance with regulatory requirements is critical to avoiding fines, penalties, and legal actions that can significantly impact a company’s reputation and financial stability. MES can help manufacturers comply with regulatory requirements by providing real-time data on production processes, enabling them to track and report on critical parameters such as temperature, humidity, and pressure. - Cost savings
One of the most significant ways MES can help manufacturers save costs is by improving productivity. MES provides real-time visibility into production processes, enabling manufacturers to identify and address bottlenecks, reduce downtime, and optimize resource utilization. By maximizing production efficiency, manufacturers can produce more products with fewer resources and reduce overall production costs.
What value does MES give to your business
Adopting an MES (Manufacturing Execution System) can drive significant value for manufacturers by improving productivity, increasing efficiency, enhancing quality, facilitating better decision-making, ensuring regulatory compliance, and reducing costs. However, to fully realize the benefits of an MES, manufacturers must carefully plan their implementation and ensure they have the necessary infrastructure, processes, and support in place.
This includes defining clear objectives, selecting the right technology solution, ensuring data integrity and security, providing adequate training and support to employees, and establishing processes to monitor and measure performance.
By taking a thoughtful, strategic approach to adopting an MES, manufacturers can position themselves for success in an increasingly competitive and rapidly evolving market.
In conclusion, MES is a powerful tool that can help manufacturers improve their operations by providing real-time visibility into production processes, optimizing resource utilization, and enhancing product quality. By leveraging MES, manufacturers can improve their efficiency, reduce costs, and make better-informed decisions. If you’re interested in implementing MES in your organization INS3 is the.
About INS3
INS3 is a System Integration company that specializes in providing Industry 4.0 technologies and solutions for industrial manufacturing, including MES (Manufacturing Execution System), SCADA (Supervisory Control and Data Acquisition), and Industrial Data Analytics. Our solutions help our clients optimize their operations by providing real-time monitoring and control of their production processes, improving efficiency, and reducing costs. With a team of experienced engineers and technicians, we work closely with our clients to design and implement customized solutions that meet their specific needs.
At INS3, we are committed to delivering high-quality products and services that exceed our clients’ expectations and help them maximize their business performance. Learn more about us and explore our services by contacting us.
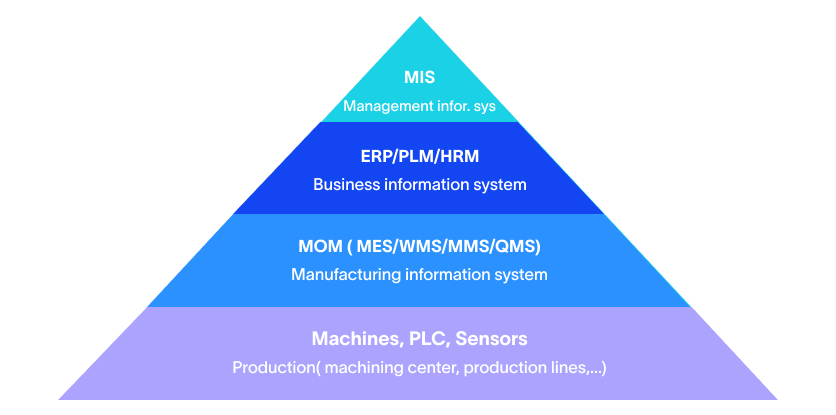
Agile MES: The Key to Unlocking Smart Manufacturing Success
MES is a computerized system used in manufacturing operations to track and document the transformation of raw materials into finished goods. An MES system typically manages and monitors work orders, equipment, materials, and personnel on the shop floor. The system provides real-time visibility into production processes, helps optimize manufacturing operations, and improves the overall efficiency of the manufacturing process.
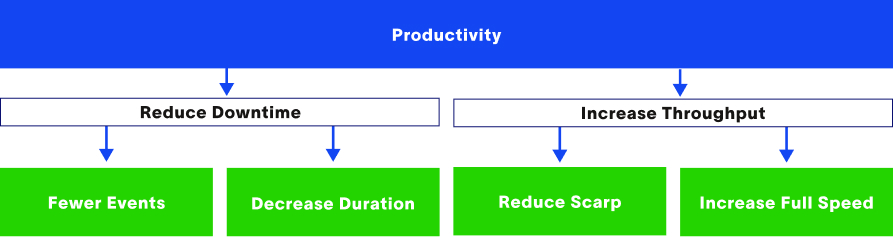
Understanding OEE: The Key to Manufacturing Efficiency
In today’s competitive manufacturing landscape, improving efficiency and productivity is crucial for businesses to remain competitive. One of the key metrics used to measure manufacturing efficiency is OEE or Overall Equipment Effectiveness. In this blog, we will take a closer look at OEE and its importance in manufacturing.
How to Effectively Conduct a Legacy System Integration
Legacy system integration can be a daunting task, but it’s a necessary one for many manufacturers that rely on outdated systems to run their business. Integrating legacy systems with modern technology can improve efficiency, streamline processes, and save time and money. However, it’s important to approach the integration process carefully and methodically to ensure success.
Share on :
Keep On Reading
Subscribe to Our Newsletter
Subscribe to our weekly newsletters to get updates regarding our new production, behind the scene process of our art creation and much more.
After submitting this form you will receive an e-mail with a confirmation link that you must click to complete your request. Detailed information on processing and cancellation can be found in our privacy policy.