7 Key Things to Implementing MES in Your Manufacturing Operations
Blog
4 Min Read
If you’re aiming to streamline your manufacturing processes, adopting a Manufacturing Execution System (MES) is the game-changer you need. MES technology bridges the gap between plant floor operations and corporate strategy, delivering real-time insights and control over your manufacturing operations. Are you curious about what is MES and how it can help your business? Find more in the blog post on our site and follow the 7 crucial steps below to ensure your MES rollout is a success.
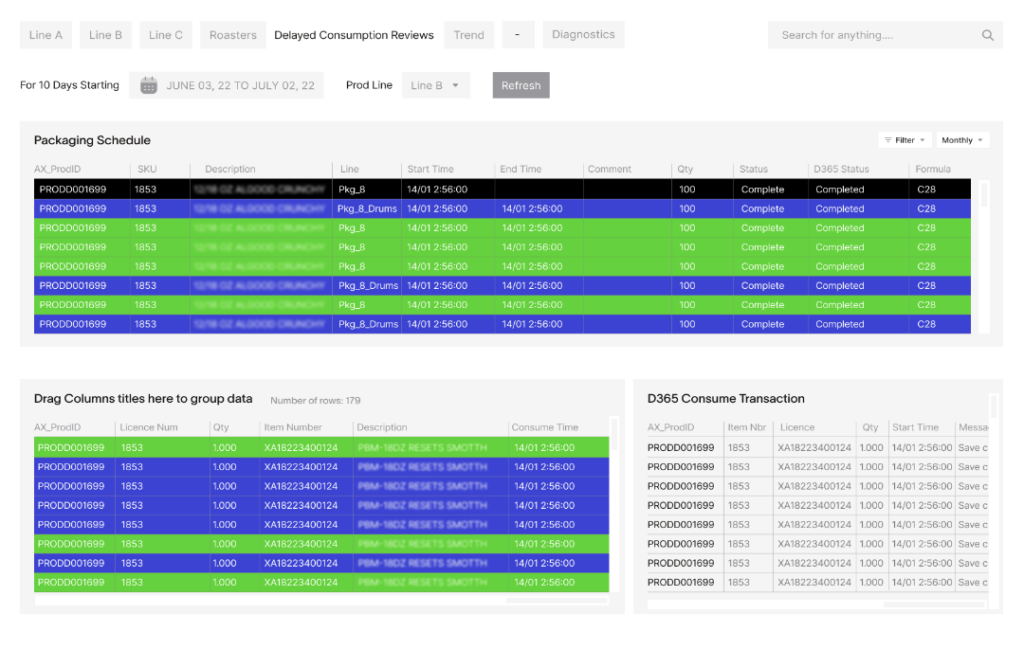
1. Assess your needs
Before you even start looking for an MES software and provider, take a step back and evaluate what you really need. What specific manufacturing challenges are you trying to observe and solve? Whether it’s reducing waste, increasing efficiency, or ensuring quality, understanding your objectives will guide your MES selection process. Engage with different specialists – from production manager to IT staff – to gather a well-rounded view of the requirements. Don’t forget, the goal here is not just to install software, but to enhance your entire manufacturing intelligence.
If you’re not sure how to start assessing your needs, give us a call for a free guided discovery call. Our discovery process begins with a meeting with key stakeholders where we delve deeper into your business challenges and discuss potential solutions.
2. Choose the right MES provider
Selecting the right MES provider is pivotal. You want a partner, not just a vendor. Look for providers with robust MES solutions and a proven track record in agile manufacturing environments. Consider their expertise in integrating intelligent systems and their ability to offer customized solutions. Don’t be shy from asking for customer references or case studies. They provide valuable insights into how the provider handles real-world manufacturing challenges.
3. Plan for integration
Seamless system integration with existing systems like ERP or supply chain management software is critical. An effective MES system should complement these systems, creating a cohesive environment. Plan the integration points carefully and ensure that your MES provider understands how to link their system with your current setup without disrupting ongoing operations. This might involve some heavy lifting in terms of data migration and system configuration, so make sure you have a clear integration roadmap from your MES provider.
4. Customize the solution
One size does not fit all in the world of MES. Customization is key to adapting the system to the specific needs of your manufacturing operations. Work with your MES provider to adjust the features and workflows of the MES to better align with your processes. Whether it’s enhancing the manufacturing information system to provide more detailed analytics or tweaking the MES program to improve user experience, customization can significantly increase the system’s efficiency and user adoption.
Check out our CoreM – Agile MES and Manufacturing system, specially engineered for user confirmability, agility, and efficiency. In a” One size does not fit all reality” we work with several leading MES vendors and work to find the best fit for your application.
5. Training and Support
Implementing a MES system is only the beginning. For the team to truly benefit, they need thorough training and additional workshops. Ensure your provider offers comprehensive training sessions and resources. Support should be proactive and responsive. This is crucial during the initial stages of post-implementation. Consider establishing a support system within your team by training selected employees to become MES experts who can then assist their colleagues.
6. Implementation strategy
Rolling out an MES system can be a complex project that requires careful planning and execution. Break down the implementation into manageable stages with clear goals and checkpoints. Monitor the process closely using specific performance indicators to evaluate the success of each stage. Address any issues promptly to keep the implementation on track. Effective project management can make the difference between a smooth rollout and a problematic one.
7. Continuous improvement and scaling
The launch of your MES system is just the starting point. As your business evolves, so should your MES. Use the gathered data to continuously refine and optimize your processes. Keep an eye on new features, upgrades and updates that could enhance functionality and solve more issues . Additionally, as your company grows, you may need to scale your MES operations – plan for this in advance to ensure that scaling up is as smooth as possible.
Final thoughts: Unlocking the next-level manufacturing efficiency with MES
Implementing MES is much more than choosing a technology – it’s a strategic move towards achieving unparalleled efficiency and quality in manufacturing operations. With the right MES system in place, you can enjoy a comprehensive view of your production activities while collecting valuable data for advanced analytics, enabling better decision-making and faster response times. But remember, the success of the MES implementation depends heavily on thorough planning, a careful selection process of the right partner, robust training and continuous improvement practices.
Ready to boost your manufacturing operations? Embrace MES and unlock the full potential of your production capabilities. Let’s start your transformative journey and pave the way for smarter and more efficient manufacturing. Get in touch to start your Digital Transformation Journey.
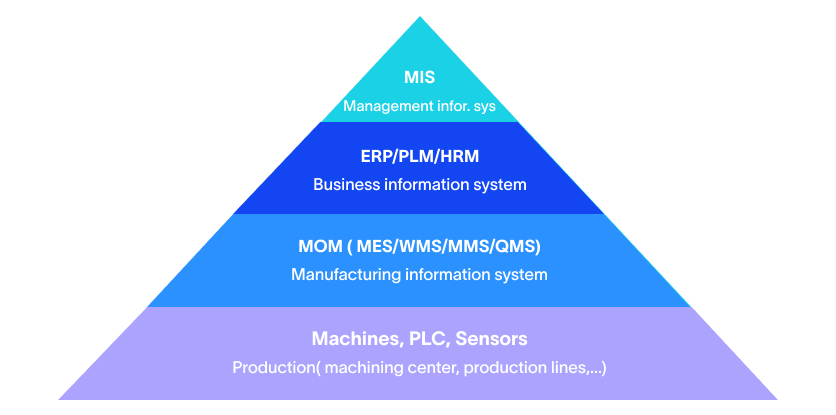
Agile MES: The Key to Unlocking Smart Manufacturing Success
MES is a computerized system used in manufacturing operations to track and document the transformation of raw materials into finished goods. An MES system typically manages and monitors work orders, equipment, materials, and personnel on the shop floor. The system provides real-time visibility into production processes, helps optimize manufacturing operations, and improves the overall efficiency of the manufacturing process.
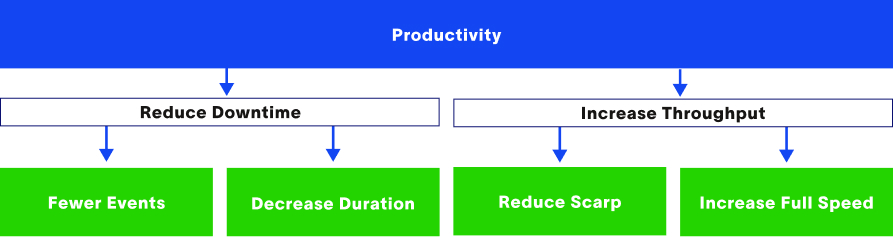
Understanding OEE: The Key to Manufacturing Efficiency
In today’s competitive manufacturing landscape, improving efficiency and productivity is crucial for businesses to remain competitive. One of the key metrics used to measure manufacturing efficiency is OEE or Overall Equipment Effectiveness. In this blog, we will take a closer look at OEE and its importance in manufacturing.
How to Effectively Conduct a Legacy System Integration
Legacy system integration can be a daunting task, but it’s a necessary one for many manufacturers that rely on outdated systems to run their business. Integrating legacy systems with modern technology can improve efficiency, streamline processes, and save time and money. However, it’s important to approach the integration process carefully and methodically to ensure success.
Share on :
Keep On Reading
Subscribe to Our Newsletter
Subscribe to our weekly newsletters to get updates regarding our new production, behind the scene process of our art creation and much more.
After submitting this form you will receive an e-mail with a confirmation link that you must click to complete your request. Detailed information on processing and cancellation can be found in our privacy policy.