Why Your MES System Is Your Secret Weapon for Manufacturing AI and Analytics
Blog
8 Min 29 Sec Read
Most manufacturers can barely scratch the surface of what their MES system can do. So, for many, it ends up functioning like an expensive MES Dashboard – a flashy display for monitoring production, but not much else. But honestly speaking, that’s a waste.
When you really connect the dots – integrating MES with time-series data historians and actually using the advanced MES features – it becomes something else entirely.
The MES system turns into the brain of your factory floor – the place where your data turns into insight… and then into action. At INS3, we have watched manufacturers go from reactive scrambling to making confident, data-backed decisions.
Here’s how.
Traditional MES Usage vs. Manufacturing Intelligence Platform
Before we talk about how you can turn your traditional MES into something more modern and polished, let’s talk about how these two differ from each other.
Build a Smarter Factory Today: Discover how Agile MES drives real-time efficiency and flexibility.
What Most Manufacturers Do – Basic Monitoring
Usually, most manufacturers use their systems to tick boxes – not drive insights. So, the generic drill they tend to follow for it is as follows –
- OEE Calculations: Tracking overall equipment effectiveness
- Production Status: Monitoring the current production runs and schedules
- Downtime Tracking: Recording the time when equipment stops working
- Basic Alarms: Alerting operators of immediate issues
- Simple Reporting: Creating end-of-shift production summaries
While this basic configuration helps you get through the day, it doesn’t allow you to reap the MES benefits properly.
Boost Productivity with the Right Metrics: Learn how OEE reveals hidden bottlenecks and opportunities.
What MES Can Really Do - Manufacturing Intelligence Engine
In contrast, organizations that harness the full potential of their MES system gain powerful operational advantages. These may include –
- Predictive Analytics: Using historical patterns to forecast quality issues and equipment failures
- Real-Time Decision Support: Collecting and providing intelligent recommendations based on current condition of your machinery
- Automated Quality Control: Integrating with inspection systems for dynamic quality management
- Supply Chain Integration: Connecting production data with materials, scheduling, and customer demands
- AI-Ready Data Pipeline: Feeding clean, contextualized information to machine learning models to make them work better
These expanded capabilities constitute the true MES benefits and transform your operations from reactive to proactive.
The Critical Link - MES + Time-Series Historians
However, to achieve the aforementioned transformation, the integration of MES with time-series data historians would be important. Here’s how to do it –
MES Provides Context:
- Product details, production times, and personnel
- Batch recipes and process parameter sets
- Quality metrics and operator inputs
- Production events and state transitions
Historians Provide Deep Data
- High-frequency sensor readings, such as temperature, pressure, and flow
- Machine performance metrics over time
- Environmenal data affecting production
- Continuous process variables and long-term trends
Together They Enable
- Correlating quality issues with specific process conditions
- Understanding how minor parameter variations affect outcomes
- Training accurate AI models with both event context and continuous data
- Implementing predictive analytics that work in production perfectly
The Hidden Superpowers: From Monitoring to Intelligence
Once you have tapped into the full potential of MES, you can use it to complete lots of tasks efficiently. Here’s what you need to know about them –
Ready to Streamline Your Production? Learn how MES brings real-time control to your shop floor.
Predictive Quality Analytics
- Traditional Approach: This method relies more on reactive testing and focuses on identifying defects only after production is complete. This delayed feedback can lead to significant waste, rework, and customer dissatisfaction.
- MES Intelligence Approach: In contrast, a modern intelligence-based approach enables manufacturers to anticipate quality issues before they arise. By combining real-time production monitoring with historical data, predictive systems can detect potential deviations in advance.
How It Works:
- The manufacturing execution system (MES) captures contextual data such as recipe parameters, operator interventions, and environmental factors.
- A time-series historian records continuous process variables, including temperature, pressure, and flow.
- AI algorithms analyze data to uncover subtle correlations that are typically imperceptible to human analysis.
- The system proactively identifies emerging quality risks and offers different types of preventive adjustments.
Example:
A food processing company discovered that flavor inconsistencies in their products were linked to specific ingredients. And the rapid temperature increases were making the entire situation even worse. Thanks to using advanced MES, their system identified this pattern four hours prior to standard quality testing to allow timely intervention.
MES Success Starts Here: Learn what every manufacturer needs to implement MES effectively.
Intelligent Root Cause Analysis
- Traditional Approach: The conventional root cause analytics usually involves manual investigation. This may include – reviewing logs, interviewing staff, and drawing assumptions. However, this approach is much more time-consuming and tends to be inconclusive more often.
- MES Intelligence Approach: An intelligence-driven MES approach allows for automated correlation of data across equipment, materials, environmental inputs, and time to identify the actual cause of anomalies.
Advanced Capabilities:
- Using pattern recognition algorithms that can pinpoint identify recurring issues
- Creating a cross-system correlation between MES even logs and historian data
- AI-powered hypothesis generation for rapid testing of probable causes
- Automated documentation of root cause and resolution paths
Example:
A chemical manufacturing facility found that product inconsistencies were not occurring due to temperature variations, as they assumed previously.
However, it was actually happening because of minor humidity fluctuations, which were occurring before production. Getting these insights was only possible due to contextualizing time-series data with MES batch records.
Bridge the Gap Between Control and Intelligence: Find out how MES transforms Ignition into a manufacturing powerhouse.
Dynamic Production Optimization
- Traditional Approach: In the case of conventional scheduling, you will have to follow some specific fixed plans with limited adaptability. When disruptions start occurring, you’ll need to make manual interruptions – which, in turn, might delay resolution and compromise throughput.
- MES Intelligence Approach: With intelligence-based systems, however, production schedules adapt dynamically based on current conditions, health of equipment, and quality forecasts. This allows for a more agile and optimized manufacturing environment.
Smart Features
- Real-time schedule adjustments based on equipment performance and availability
- AI-driven forecasting to allocate resources efficiently
- Dynamic routing based on in-process quality trends
- Integration of predictive maintenance to prevent unplanned downtime
The result, in the end, is a proactive, data-informed production model that significantly contributes to improving manufacturing efficacy.
Manufacturing Data Orchestration for AI
- The Power of Integration: When integrated effectively, manufacturing execution systems can evolve into centralized intelligence platforms that unify operational data. Their value grows exponentially when connected with time-series historians to form a comprehensive data ecosystem.
Data Orchestration Capabilities:
- Standardized, structured datasets optimized for machine learning models
- Real-time data flow to edge analytics devices and cloud platforms
- Richly contextualized records that enhance AI training accuracy
- Automated data validation and cleansing to ensure high-quality insights
AI Readiness Through MES-Historian Integration:
- Clean, labeled datasets that combine event-based and continuous process data
- Direct deployment of predictive models into production workflows
- Seamless alignment between AI-generated insights and human-machine interfaces
- Ongoing model refinement through live production feedback.
MES + AI: The Foundation for Industry 4.0
At its core, Industry 4.0 technology isn’t simply about machines talking to each other. It’s more about cultivating intelligent and adaptive systems that can make smart decisions at scale. When manufacturing execution systems are connected to a time-series historian, they become much more than just another tracking tool.
Is Your Operation Running at Full Potential? See how MES and SCADA upgrades unlock new levels of productivity.
Autonomous Manufacturing Enablement
- Self-Optimizing Processes: AI models, which are trained on historical data from MES logs and continuous sensor streams – can fine-tune process parameters in real life perfectly.
- Predictive Maintenance Integration: Instead of reacting to breakdowns, equipment health models combine contextual MES insights with historian-driven metrics to foresee and prevent failures.
- Quality Prediction: Real-time forecasting helps anticipate product quality issues before they occur, which may cut down waste and rework.
- Supply Chain Responsiveness: The system adapts production to account for raw material fluctuations, bottlenecks, or shifting customer demands.
Enhanced Human-Machine Collaboration
- Intelligence Operator Guidance: AI-generated suggestions are embedded into the MES dashboard and allow operators to make faster and more informed decisions without digging into too much data.
- Augmented Decision Making: Predictive insights blend with historical performance data to guide your technicians and managers more confidently.
- Continuous Learning: Every adjustment and decision you make – whether it’s automated or manual – feeds back into the system. Over time, the system will learn, evolve, and become more effective.
Cross-System Intelligence
- ERP Integration: Production intelligence flows seamlessly into enterprise planning, improving forecasting accuracy, and operational agility.
- Quality Systems: Feedback from inspection processes loops directly into production via MES, tightening quality control at every stage.
- Maintenance Systems: Predictive maintenance insights are pushed into CMMS platforms, aligning shop floor needs with maintenance schedules.
The combination of these features leads to tangible MES benefits, which includes higher throughput, reduced downtime, improved quality, and more adaptive operations.
INS3's MES Intelligence Methodology
At INS3, we don’t just implement MES, we evolve it. Our structured methodology turns the MES platform into a true manufacturing intelligence engine. It also becomes capable of driving real business outcomes.
This transformation usually unfolds in three key phrases –
MES Potential Assessment
This first step is all about understanding where your current system stands. Our team starts by assessing how well existing MES features are being used and evaluate the overall quality of data being generated.
If a historian system is already in place, we will review how data flows and whether those flows are optimized or not. AI readiness is another critical checkpoint we focus on to check if the current architecture can support advanced analytics or not.
Finally, we perform a detailed gap analysis to uncover what’s missing and where your system’s untapped potential lies.
Ready to Scale Smarter? Unlock the production gains of MES software today.
Intelligence Foundation Building
Once the baseline is clear, we start focusing on building a stable, intelligent foundation. This means creating reliable links between the MES and time-series historians – which ensures that context-rich events work perfectly with high-frequency sensor data.
From there, our team standardizes data models so that information is consistent, accurate, and usable across systems. Often, companies already own unused capabilities – so we activate those dormant analytics-ready modules too.
AI and Analytics Implementation
With the groundwork in place, it’s time to put intelligence into action.
We start small – with targeted, high-impact analytics pilots like predictive quality or performance forecasting. AI models are developed using the enriched datasets generated by the MES-historian integration.
Once validated, these models are embedded directly into the MES workflows – meaning operators interact with AI insights through the familiar MES Dashboard.
Of course, no rollout is complete without people. So, we invest in training, helping teams fully embrace AI-assisted decision-making.
Real Success Story
- Challenge: A pharmaceutical manufacturer’s MES system tracked batch events but couldn’t predict quality variations. Even if they initiated extensive quality testing, they still couldn’t find anything.
- Solution: INS3 integrated their MES with time-series historians and implemented predictive quality analytics.
Implementation
- Connected MES batch context with continuous process data from historians
- Developed AI models correlating recipe parameters with quality outcomes
- Integrated predictions into MES operator interfaces
- Established feedback loops for continuous model improvement
Results
- 25% reduction in out-of-specification batches
- 40% faster root cause analysis for quality issues
- 15% improvement in overall process efficiency
- ROI achieved within 8 months
Getting Started: Your MES Intelligence Roadmap
If you are thinking about upping the intelligence of your MES program, this section is custom-made for you. So, let’s get started with it –
Quick Assessment Questions
- Data Integration: Is your MES connected to process historians, or are they still operating in the silos?
- Feature Utilization: Are you going beyond the basics and unlocking advanced MES features that support real-time decisions?
- Analytics Readiness: Can you extract contextualized data without friction, or does it still require manual effort?
- AI Preparation: Is your data clean, structured, and comprehensive enough to support machine learning initiatives?
Implementation Roadmap
The entire implementation process will take around six months to complete. Let’s keep reading to know more about what the roadmap for the same entails.
Months 1-2: Foundation Assessment
So, firstly, you have to start by auditing current setup and ask yourself –
- How well does your MES interact with your historians?
Once you have information on this, you can start pinpointing analytics opportunities with the highest potential impact. It’s also a god time to define baseline metrics so you know what ‘improvement’ actually looks like.
Months 3-4: Integration Enhancement
In the third and fourth month, you will have to focus on how data flows.
For that, you’ll have to fine-tune MES-historian integration and activate the more advanced capabilities already built in your system. This phase is also where you’ll have to prepare your data infrastructure to support intelligent applications down the line.
Months 5-6: Intelligence Plot
Finally, you are ready to deploy your first AI or analytics use cases – predictive quality and equipment performance forecasting. You can use the MES Dashboard to surface AI insights directly to your operators. Just make sure they’re trained, confident, and ready to act on what the system recommends.
Best Practices for Improving Manufacturing Efficiency
- Don’t skip the foundation – solid MES-historian integration is key before layering on AI
- Choose different use cases where fast decisions matter; that’s where real-time value shines as well
- Make sure operators understand the ‘why’ behind AI suggestions – it builds trust
- Create feedback loops so your system can learn and improve over time
- Keep your data clean, your governance strong, and your system secure
Your MES: From Dashboard to Manufacturing Brain
Your MES system isn’t just another piece of software.
It’s potentially the operational brain behind your entire plant. When tightly integrated with time-series historians and enhanced with AI, it evolves beyond passive oversight and becomes a real-time manufacturing intelligence platform.
The truth is, the most competitive manufacturers today aren’t simply collecting data—they’re putting it to work.
They’re translating signals from machines, processes, and people into timely, informed decisions. And that’s what drives smarter, faster, and more resilient operations.
At INS3, we help manufacturers tap into the real value hiding in plain sight. For many, their MES is already capable—it just hasn’t been pushed far enough.
With the right strategy, we transform underused systems into intelligent hubs of operational insight. The result?
Measurable outcomes – from quality gains to more agile production, rooted in the real-world MES Benefits you’ve been promised but maybe never fully unlocked.
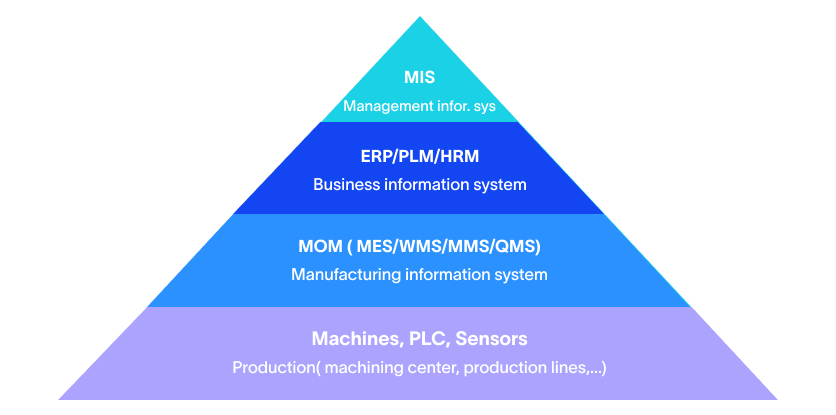
Agile MES: The Key to Unlocking Smart Manufacturing Success
MES is a computerized system used in manufacturing operations to track and document the transformation of raw materials into finished goods. An MES system typically manages and monitors work orders, equipment, materials, and personnel on the shop floor. The system provides real-time visibility into production processes, helps optimize manufacturing operations, and improves the overall efficiency of the manufacturing process.
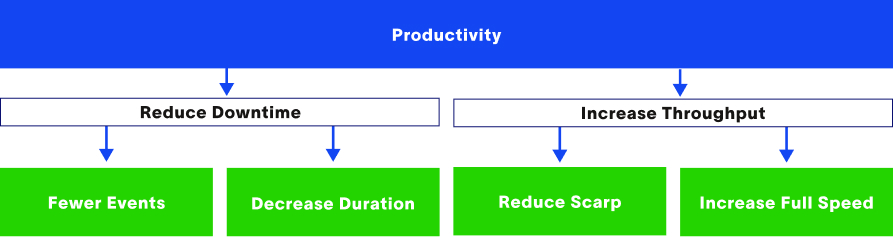
Understanding OEE: The Key to Manufacturing Efficiency
In today’s competitive manufacturing landscape, improving efficiency and productivity is crucial for businesses to remain competitive. One of the key metrics used to measure manufacturing efficiency is OEE or Overall Equipment Effectiveness. In this blog, we will take a closer look at OEE and its importance in manufacturing.
How to Effectively Conduct a Legacy System Integration
Legacy system integration can be a daunting task, but it’s a necessary one for many manufacturers that rely on outdated systems to run their business. Integrating legacy systems with modern technology can improve efficiency, streamline processes, and save time and money. However, it’s important to approach the integration process carefully and methodically to ensure success.
Share on :
Keep On Reading
Subscribe to Our Newsletter
Subscribe to our weekly newsletters to get updates regarding our new production, behind the scene process of our art creation and much more.
After submitting this form you will receive an e-mail with a confirmation link that you must click to complete your request. Detailed information on processing and cancellation can be found in our privacy policy.